بررسی انواع آسیب تسمه نقاله و علل بهوجودآمدن آنها
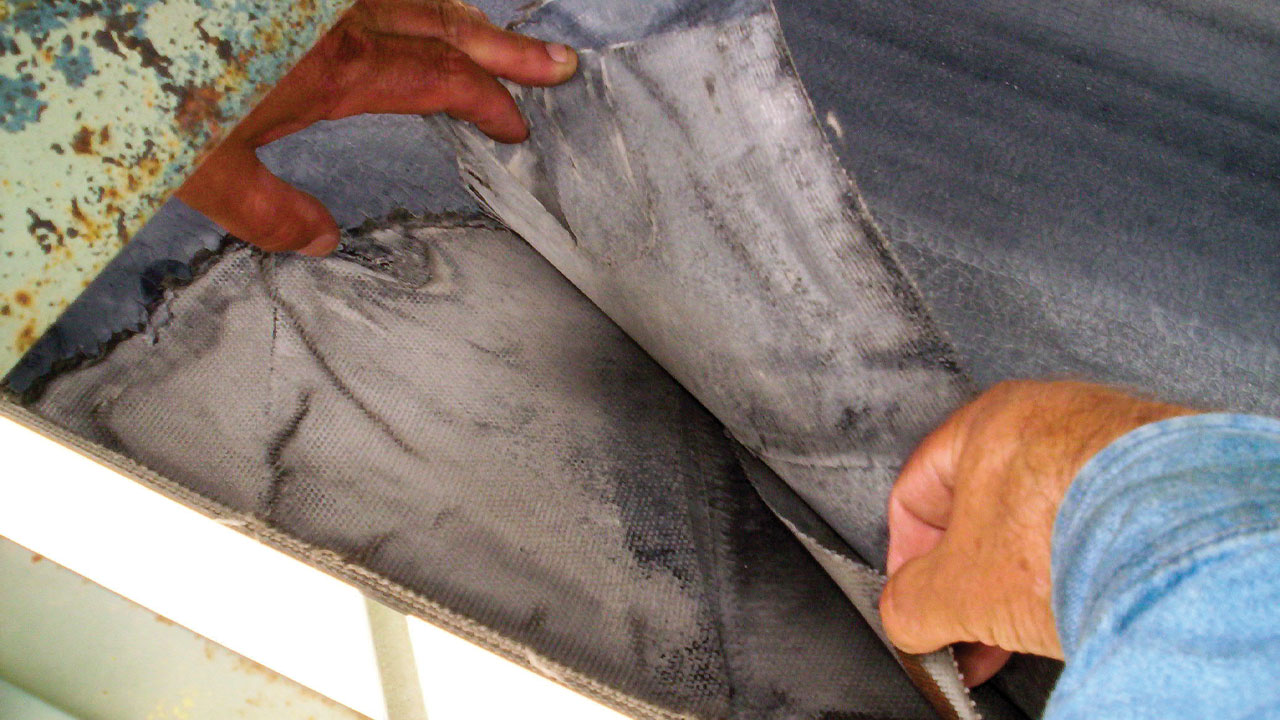
تسمه نقاله مهمترین قسمت در عملکرد هر سیستم نوار نقاله است. آسیبهای وارده به این عنصر باعث توقفهای پرهزینه در سیستم انتقال مواد میشود. آسیب تسمه نقاله میتواند به علت شرایط کاری یا تماس با موادی که حمل میشود باشد. عملکرد صحیح میتواند راهی برای افزایش مؤثر عمر سرویسدهی تسمه نقاله باشد. تجربه نشان میدهد که اکثر آسیبهای وارده به تسمه نقاله به دلیل عملکرد نامناسب سیستم نوار نقاله یا وضعیت فنی قطعات (رولیک، اسکریپر و …) است. در این متن انواع آسیبهای وارده به تسمه نقاله (جدای از کیفیت خود تسمه نقاله) بررسی میشود. البته لازم به ذکر است که برای عملکرد مناسب سیستم نقاله کیفیت تسمه نقاله بسیار مهم است. عمر تسمه نقاله به چندین فاکتور مهندسی، سازهای و عملیاتی بستگی دارد. به علت استفاده نامناسب اغلب تسمهنقالههای موجود قبل از استفاده بهینه کنار گذاشته میشوند. تسمه نقاله بیشتر از بقیه اجزا در معرض سایش است که ناشی از شرایط کاری، حرکت مداوم، تماس با مواد مورد حمل و یا اجزای دوار (عمدتاً رولیک) میباشد. آسیب تسمه نقاله منجر به توقفها و تعمیرات پرهزینه میشود. همچنین تغییر در جریان مواد و بارهای متغیر نیز باعث آسیب به تسمه نقاله میشوند. در حال حاضر، تعیین درجه سایش تسمه نقاله در طول زمان، میتواند بر اساس اندازهگیریهای دورهای ضخامت تسمه انجام میشود. نوع آسیب به تسمه نقاله به عواملی مثل فاکتورهای سازهای، نوع مواد مورد حمل و شرایط عملیاتی بستگی دارد. آسیبهای وارد به تسمه نقاله را میتوان به دو گروه اصلی تقسیمبندی کرد:
- آسیبهای موضعی که در قسمتی از تسمه نقاله رخ میدهد و با چشم غیرمسلح نیز قابل تشخیص است.
- آسیبهای خطی که در تمام طول تسمه نقاله رخ میدهد.
در بخش زیر به انواع آسیبهای معمول تسمه نقاله و علائم آن اشاره خواهد شد:
- انحراف تسمه نقاله
تمایل تسمه نقاله برای حرکت به سمت لبهها را میتوان انحراف تسمه نقاله تعریف کرد. این نوع آسیب میتواند متداولترین آسیبها به تسمه نقاله باشد. این مشکل هم بهعنوان علت آسیب تسمه نقاله مطرح شود هم بهعنوان معلول آن. دلایل انحراف تسمه نقاله را به شکل کاملی در مقاله دیگر بررسی نمودهایم. در شرایط عادی عملکرد، تسمه نقاله نسبت به محور طولی نوار نقاله متقارن است و تراز است. انحراف تسمه نقاله علاوه بر اینکه خطرهای جانی برای اپراتورها دارد باعث خوردگی سازه سیستم نوار نقاله و همچنین ساییدگی لبههای تسمه نقاله میشود.
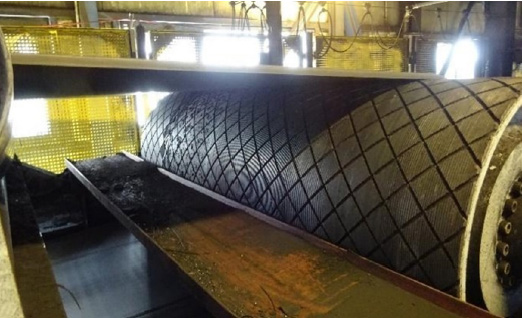
شکل 1 انحراف تسمه نقاله روی درام متحرک
- سایش نامتقارن رولیکها و درام
سایش نامتقارن عناصر دوار سیستم نوار نقاله مستقیماً به دلیل نقص خود تسمه نقاله نیست، ولی در مدتزمان طولانی میتواند تأثیر زیادی در تسریع فرایند سایش تسمه نقاله داشته باشد.
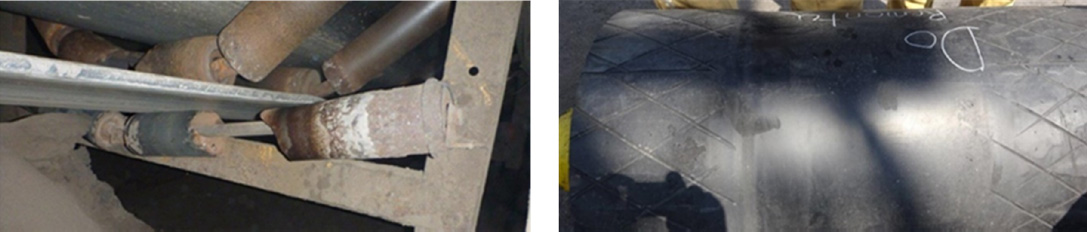
شکل 2 سایش نامتقارن در اعضای دوار. سایش تیوب رولیک (چپ) و سایش پولی لگینگ (راست)
حالتهای سایش عناصر دوار سیستم نوار نقاله بسیار متنوع است. نقص در عملکرد رولیکها و درام (مثل گیرکردن رولیکها) حتی میتواند باعث خطر آتشسوزی شود. ساییدگی و خرابی در سطح فلزی رولیکها نیز خطرناک است. در این حالت قسمت آسیبدیده میتواند مثل یک تیغه باعث بریده شدن تسمه نقاله شود و استفاده مجدد از آن تسمه را غیرممکن سازد. ساییدگی لبههای تسمه نقاله باعث میشود عرض تسمه نقاله کاهش یابد. این مورد باعث میشود که تنش کششی وارد شده به تسمه نقاله افزایش یابد و باعث کاهش طول عمر آن میشود. تجمع گردوغبار لاستیکی روی سازه سیستم نوار نقاله نشان میدهد که روکشهای تسمه نقاله توسط عناصر متحرک ساییده شدهاند. این یک پدیده طبیعی است که ناشی از ماهیت برهمکنش تسمه نقاله-رولیک است، جایی که لوله غلتکی معمولاً بهعنوان یک ماده ساینده عمل میکند. برای عملکرد استاندارد یک سیستم نوار نقاله، این پدیده نباید تشدید شود، بلکه به طور سیستماتیک در طول زمان توزیع شود. به همین دلیل، افزایش ناگهانی ساییدگی تسمه نقاله میتواند مبنایی برای یافتن نقص در عملکرد سیستم باشد.
- سایش پوشش لاستیکی
روکشها و لبههای تسمه نقاله در معرض سایش قرار دارند. فرایند ساییدگی یک پدیده طبیعی است که در نتیجه برهمکنش تسمه نقاله با درام، هرزگردها و مواد حملشده به وجود میآید. نوع طراحی و وضعیت لوله غلتکی اهمیت زیادی در فرایند ساییدگی روکش دارد. سایش دو ماده بهسختی آنها بستگی دارد، بنابراین سایش بین لاستیک – لاستیک و لاستیک – فولاد ویژگیهای متفاوتی خواهند داشت. خوردگی لوله غلتکی روند تخریب پوشش لاستیکی تسمه نقاله در حال کار را تسریع میکند.
- سوراخشدن و برش پوشش لاستیکی
مقاومت در برابر سوراخشدن تسمه نقاله یکی از معیارهای مهم برای ارزیابی دوام آن است. بیشتر خرابیهای تسمه نقاله با سوراخشدن یا بریدن تاپ کاور همراه است. در مورد تسمهنقالههای استیل کورد یک نشانه خاص از آسیب میتواند بروز آثار خوردگی روی آن باشد. تخریب پوشش لاستیکی میتواند باعث نفوذ عوامل مخرب به داخل تسمه نقاله گردد.
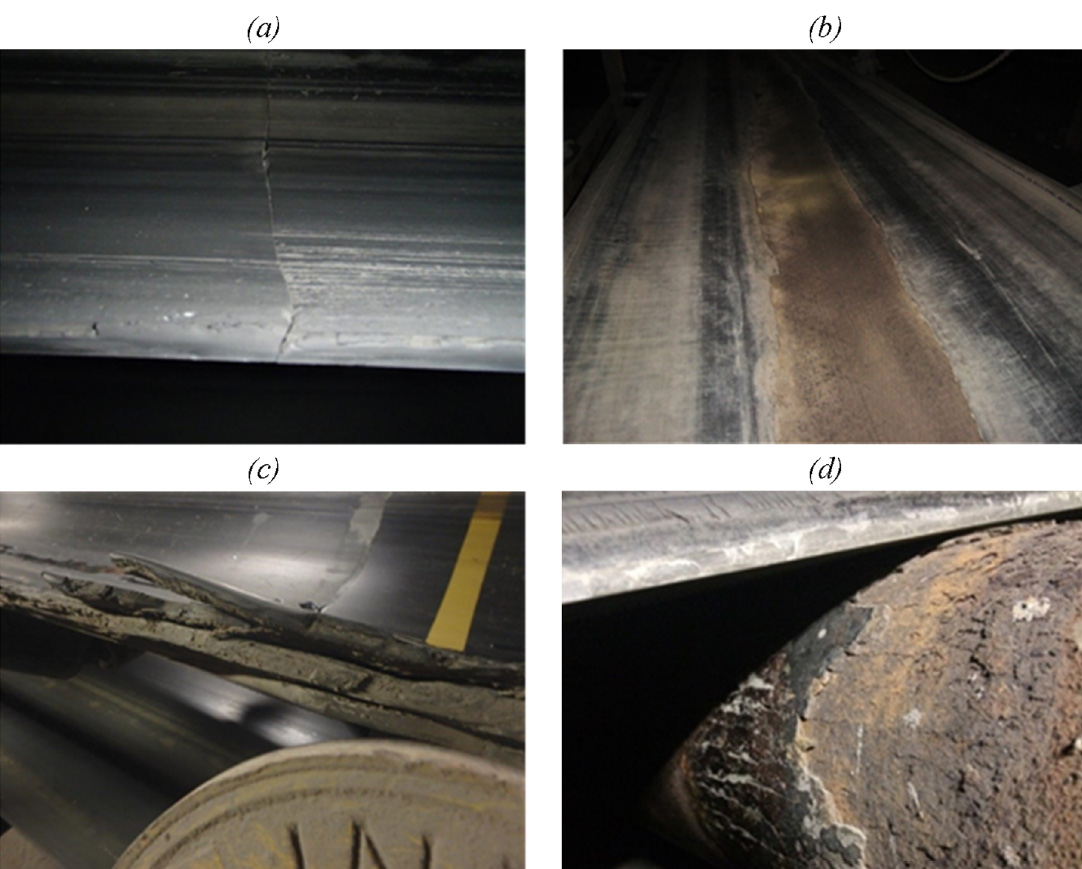
شکل 3 خوردگی کاور پایین (a)،خوردگی کاور بالا (b)، خوردگی لبهها (c)،خوردگی دراجزی دوار(d)
- برش طولی تسمه نقاله
بریدگیهای طولی یکی از مخربترین آسیبهاست که میتواند باعث از کارافتادگی تسمه نقاله شود. ایجاد بریدگیهای طولی معمولاً یک اتفاق ناگهانی است؛ بنابراین رصد علائم برای پیشبینی آن دشوار است. درنظرگرفتن عوامل بالقوه ایجاد برش میتواند کمککننده باشد.
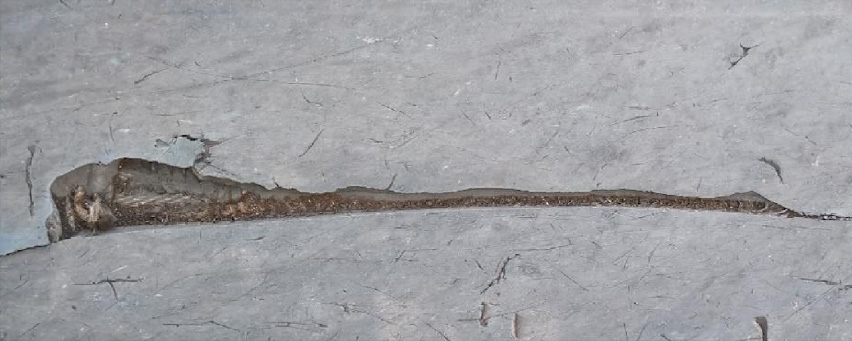
شکل 4 برش طولی در تسمه نقاله
- ازبینرفتن چسبندگی پوشش و خرابی پوشش
نوع دیگری از آسیب، لایهلایه شدن ساختار تسمه نقاله است که گاهی به آن ترکخوردگی روکش نیز میگویند. این شامل جداشدن پوشش لاستیکی از عوامل تقویتکننده (منجید و کورد فلزی) است. این اتفاق به طور چشمگیری روند سایش را تسریع میکند و درعینحال استحکام تسمه نقاله را کاهش میدهد. این اتفاق میتواند ناشی از اشتباهات فاحش در طراحی سیستم نوار نقاله (مثل قطر درام خیلی کوچک)، کاهش پارامترهای عملیاتی تسمه نقاله (سرعت، تنشن و …) و یا مشکل ذاتی تسمه نقاله (ایراد در ساخت) باشد.
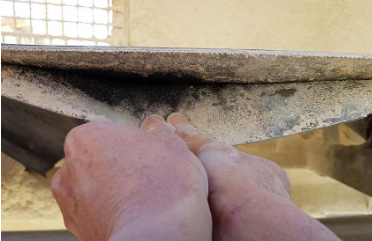
شکل 5ازبینرفتن چسبندگی پوشش
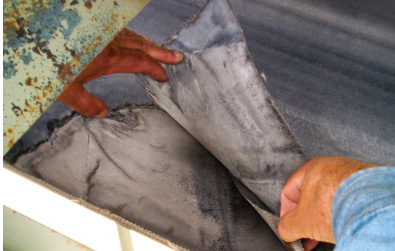
- شکستن کاور، لایهها، یا بیرونزدن کورد فلزی
استفاده از تسمه آسیبدیده یا تسمهنقالهای که بهدرستی تعمیر نشده است ممکن است منجر به ایجاد آسیب شود. همچنین این کار باعث افزایش خطر گیرکردن تسمه نقاله به عناصر دوار (به دلیل برآمدگی و اجزای محافظت نشده تسمه نقاله آسیبدیده) میشود. اقدامات سریع جهت ترمیم آسیب یا جایگزینی قطعات آسیبدیده تسمه نقاله میتواند منجر به بهبود طول عمر کار تسمه شود.
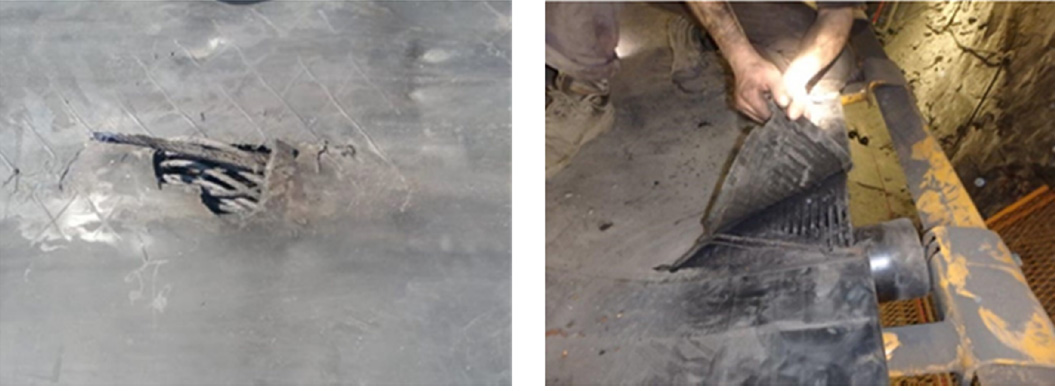
شکل 6 آسیب منطقه ای در تسمه نقاله، بیرونزدن کورد فلزی (چپ) و پارگی کاور لاستیکی (راست)
- ازبینرفتن چسبندگی کوردهای فلزی
ظاهر برآمده روی سطح تسمه نقاله ممکن است نشاندهنده ازبینرفتن چسبندگی بین کوردهای فلزی و لاستیک باشد. این مشکل باعث ازبینرفتن خواص تسمه نقاله، تضعیف ساختار و تسریع سایش آن میشود. در این حالت وضعیت کشش تسمه نقاله نیز تغییر میکند. در حالت بدتر کوردهای جدا شده میتواند باعث ایجاد بریدگی در کاور تسمه نقاله گردد.
- صدای زیاد، نامنظم، محلی و لرزش سیستم انتقال مواد در هنگام کار
نهتنها در سیستم نقاله، برای هر ماشینی صدا و لرزش از علائم بسیار مهم نحوه عملکرد آن است. صدا و لرزش را نمیتوان مستقیماً بهعنوان آسیب تسمه نقاله دستهبندی کرد، اما آنها میتوانند نشاندهنده نقص در عملکرد بعضی قطعات باشند. بروز صدا و لرزش محلی معمولاً با اختلال در عملکرد عادی سیستم همراه است که میتواند منجر به آسیب به تسمه نقاله گردد. هرگونه صدا و لرزش اضافی میتواند کمک زیادی در یافتن نقص عملکرد قطعات کند و میتوان با اقدامات پیشگیرانه از آسیب تسمه نقاله جلوگیری کرد.
در این بخش به عواملی که باعث ایجاد آسیب در تسمه نقاله میشود ذکر میشود:
در بسیاری از موارد، سایش زودرس ناشی از عوامل خارجی است. باتوجهبه ماهیت برهمکنش بین تسمه نقاله و عناصر دوار سیستم نقاله و شرایط عملیاتی مختلف، هر یک از آسیبهایی که قبلاً اشاره شد ممکن است دلایل زیادی داشته باشند. با درنظرگرفتن عواملی مثل جنبههای طراحی، کیفیت اجزاء، بهویژه عناصر دوار، و همچنین تعمیر و نگهداری، منابع اصلی آسیب به تسمه نقاله را میتوان به سه گروه اصلی تقسیم کرد.
- عوامل ناشی از طراحی و ساخت سیستم نوار نقاله
- زاویه برآمدگی لبهها: گروه اول عوامل آسیب ناشی از طراحی یا ساخت سیستم نقاله هستند. متداولترین زوایای برآمدگی لبهها از 15 تا 45 درجه است. به علت ایجاد تمرکز تنش در نقاط تماس با رولیک مرکزی و در نقاط فرورفتگی این محل جایی است که بیشترین احتمال رخدادن آسیب وجود دارد. پارامتر تعیینکننده توانایی تسمه نقاله برای دوامآوردن در چنین حالتی، انعطافپذیری عرضی و سفتی آن است. ضروری است که تسمه نقاله در تماس کامل با تمام رولیکها باشد. درصورتیکه زاویه برآمدگی بزرگ باشد شیب لبه نیز زیاد خواهد بود که این مورد بر عمر پوسته رولیکها و تسمه نقاله تأثیر منفی میگذارد. در شکل زیر زاویه برآمدگی لبهها با (Belt trough angle) نشان داده شده است.
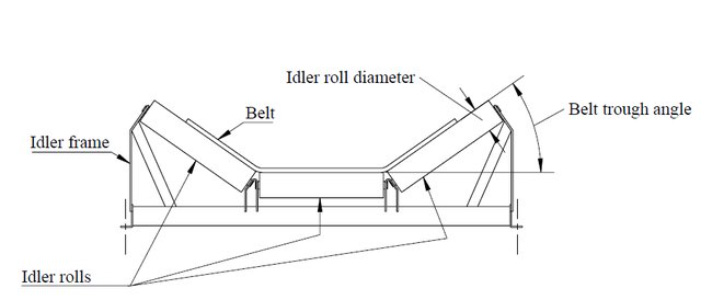
شکل 7 زاویه برآمدگی
- فاصله بین رولیکها: در نقاطی از پایه رولیک که رولیکها با هم فاصله دارند و شکاف وجود دارد تسمه نقاله خم میشود. تسمهنقالهای که به هر دلیلی خم شده است نسبت به یک تسمه نقاله مسطح متحمل تنشهای اضافی در نقاط خمش میشود. هنگامی که تسمه خم میشود در لایههای بالای تسمه نقاله تنشهای فشاری و در لایههای پایین تنشهای کششی ایجاد میشود. مقدار این تنش به عواملی همچون زاویه برآمدگی، خواص تسمه و وزن محموله روی تسمه بستگی دارد. تنشهای کششی در لایههای پایین تسمه نقاله میتواند منجر به ایجاد ترک در سطح تسمه نقاله شود. این ترکهای سطحی میتوانند در تمام طول مسیر تسمه نقاله ایجاد شوند و خسارات بیشتری ایجاد کنند. در نقاط تماس با رولیک، تسمه نقاله تحت تنشهای فشاری ناشی از جرم مواد حمل شده قرار میگیرد. فاصله بسیار زیاد بین رولیکها باعث افزایش تنشها در محل تماس رولیک با تسمه نقاله میشود. در این حالت لبههای رولیک مانند یک تیغ میتواند به تسمه نقاله آسیب وارد کند. فاصله بین رولیکها نباید از 10 میلیمتر بیشتر باشد.
- فاصله بین رولیکها: در نقاطی از پایه رولیک که رولیکها با هم فاصله دارند و شکاف وجود دارد تسمه نقاله خم میشود. تسمهنقالهای که به هر دلیلی خم شده است نسبت به یک تسمه نقاله مسطح متحمل تنشهای اضافی در نقاط خمش میشود. هنگامی که تسمه خم میشود در لایههای بالای تسمه نقاله تنشهای فشاری و در لایههای پایین تنشهای کششی ایجاد میشود. مقدار این تنش به عواملی همچون زاویه برآمدگی، خواص تسمه و وزن محموله روی تسمه بستگی دارد. تنشهای کششی در لایههای پایین تسمه نقاله میتواند منجر به ایجاد ترک در سطح تسمه نقاله شود. این ترکهای سطحی میتوانند در تمام طول مسیر تسمه نقاله ایجاد شوند و خسارات بیشتری ایجاد کنند. در نقاط تماس با رولیک، تسمه نقاله تحت تنشهای فشاری ناشی از جرم مواد حمل شده قرار میگیرد. فاصله بسیار زیاد بین رولیکها باعث افزایش تنشها در محل تماس رولیک با تسمه نقاله میشود. در این حالت لبههای رولیک مانند یک تیغ میتواند به تسمه نقاله آسیب وارد کند. فاصله بین رولیکها نباید از 10 میلیمتر بیشتر باشد.
- پولی لگینگ: پولی لگینگ سرامیکی قطعاً در برابر سایش مقاومتر از پولی لگینگ معمولی هستند. علاوه بر این، آنها مقادیر بالاتری از ضریب اصطکاک را ارائه میدهند. الگوی روی سطح پولی لگینگ برای بالابردن ضریب اصطکاک بین تسمه و درام انتخاب میشوند. در حالت معمول پولی لگینگ از لبهها کوچک تیز برای ازبینبردن لغزش بین تسمه و درام استفاده میشود. این لبههای تیز روی تسمه نقاله میتواند باعث تسریع سایش تسمه نقاله شود.
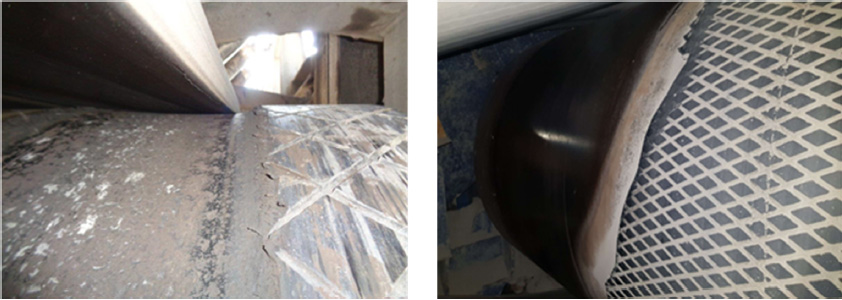
شکل 8 سایش پولی لگینگ
- انتخاب اشتباه تسمه نقاله: انتخاب تسمه نقاله با ضخامت مناسب و پارامترهای مناسب ازنقطهنظر حرکت تسمه بر روی پایه رولیک و تطابق اصطکاکی تسمه و عناصر دوار مهم است. نوع تسمه نقاله باتوجهبه عواملی همچون طول نوار نقاله، سرعت تسمه نقاله، عرض تسمه نقاله، نوع رولیکها، نوع مواد حمل و … انتخاب میشود. مهمترین مسئله در تنظیم پارامترهای مناسب یک تسمه، انتخاب صحیح استحکام کششی تسمه مطابق با شرایط ایمنی است. در حال حاضر برای تعیین ضریب ایمنی استحکام کششی تسمهنقالهها از استاندارد DIN22101 و استانداردهای CEMA استفاده میشود. هنگام انتخاب تسمه استحکام تاپ کاور تسمه نقاله نیز مهم است. تاپ کاور باید در برابر لبههای تیز مواد و اثر ساینده آن مقاوم باشد.
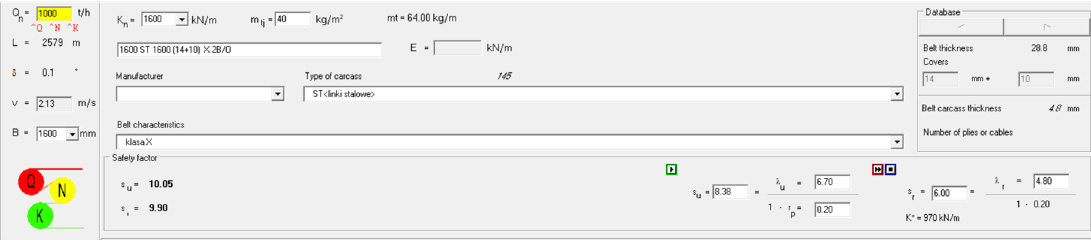
شکل 9 انتخاب تسمه نقاله با استفاده از نرم افزار
طول ترانزیشن کم: نقطه بحرانی هر سیستم نوار نقاله قسمت ترانزیشن آن است. (ترانزیشن فاصلهای است که تسمه نقاله که زاویه برآمدگی دارد به تسمه نقاله صاف تغییر مییابد). تغییر در سطح مقطع تسمه نقاله باعث تغییر در توزیع تنش تسمه نقاله میشود. طول ترانزیشن مناسب در استانداردها تعریف شده است. فشار غیرمتعارف در محل درام منجر به تسریع سایش پولی لگینگ بخصوص در لبهها و در نتیجه افزایش نرخ سایش کاور تسمه نقاله میشود. در موارد شدیدتر اگر الاستیسیته تسمه کم باشد و طول ترانزیشن بهصورت مناسب طراحی نشده باشد منجر به تغییر شکل تسمه نقاله (belt cupping) میشود.
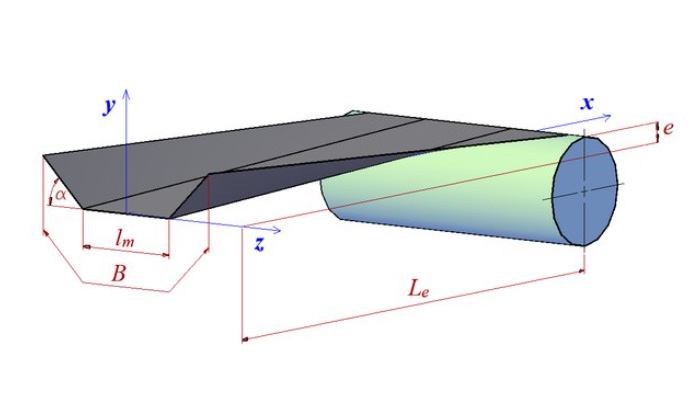
شکل 10 فاصله ترانزیشن(Le)
- قطر درام نامناسب: انتخاب نامناسب قطر درام بر دوام تسمه نقاله تأثیر منفی میگذارد. به طور معمول، تسمهنقالههای با استحکام بالا با سفتی بیشتر مشخص میشوند، بنابراین به درامهایی با قطر بزرگتر نیاز دارند. در هنگام خمش تسمه نقاله، نیروهای کششی در داخل کورد فلزی (یا منجید) و تاپ کاور، نیروی فشاری در کاور پایین ایجاد میشود. در مورد تسمهنقالههای منجیدی چندلایه، خمشدن تسمه نقاله روی درام با قطر کوچک، احتمال لایهلایه شدن تسمه نقاله (به علت توزیع نابرابر نیروهای کششی یا فشاری در لایهها) را ایجاد میکند. این تغییر نیرو عناصر سازنده تسمه نسبت به یکدیگر (توزیع نابرابر نیرو در لایهها در هنگام عبور از درام) باعث ایجاد خستگی در این عناصر و در نتیجه تخریب میشود و هرچقدر قطر درام کوچکتر از حالت استاندارد باشد این تخریب سریعتر اتفاق میافتد. در مورد تسمهنقالههای استیل کورد کشش در کوردهای فلزی ممکن است باعث ازبینرفتن کاور پایین شود. در برخی مواقع اگر خمش تسمه بیش از حد باشد نیروی ایجاد شده روی کوردهای فلزی میتواند پوشش پلاستیکی را از بین ببرد.
- شوت نامناسب: شوت نقطهای از تسمه نقاله است که در آن بیشترین خطر خرابی وجود دارد؛ بنابراین باید استانداردهای تعریف شده در طراحی شوت در نظر گرفته شود. ایستگاه بارگیری باید بهگونهای طراحی شده باشد که مواد بهراحتی جریان یابد و مقاومتی در برابر جابهجایی نداشته باشد. لازم به یادآوری است که سرعت مواد بارگیری باید با سرعت تسمه نقاله برابر باشد. نقطه بارگذاری ضعیف ممکن است منجر به وقوع بسیاری از حوادث نامطلوب شود، بهعنوانمثال آسیب مکانیکی ناشی از سقوط تودههای بزرگ که از ارتفاع سقوط میکنند و میتواند منجر به بریدگی تسمه نقاله شوند. مسدودشدن شوت باعث خرابی ناگهانی میشود که در موارد شدید میتواند منجر به آسیب دائمی به تسمه نقاله مثل برش طولی آن شود. انسداد شوت، جزء خرابیهای خطرناکی در تسمه نقاله است که اغلب منجر به تخریب کامل تسمه میشود، مگر اینکه سیستم فوراً متوقف شود. پس از چنین توقفی، تسمه نقاله را بادقت راهاندازی کنید و وضعیت تسمه را در تمام طول مسیر بررسی نمایید. توزیع ناهموار مواد روی تسمه، میزان سایش نامنظم تسمه و مقاومت در برابر حرکت را تشدید میکند.
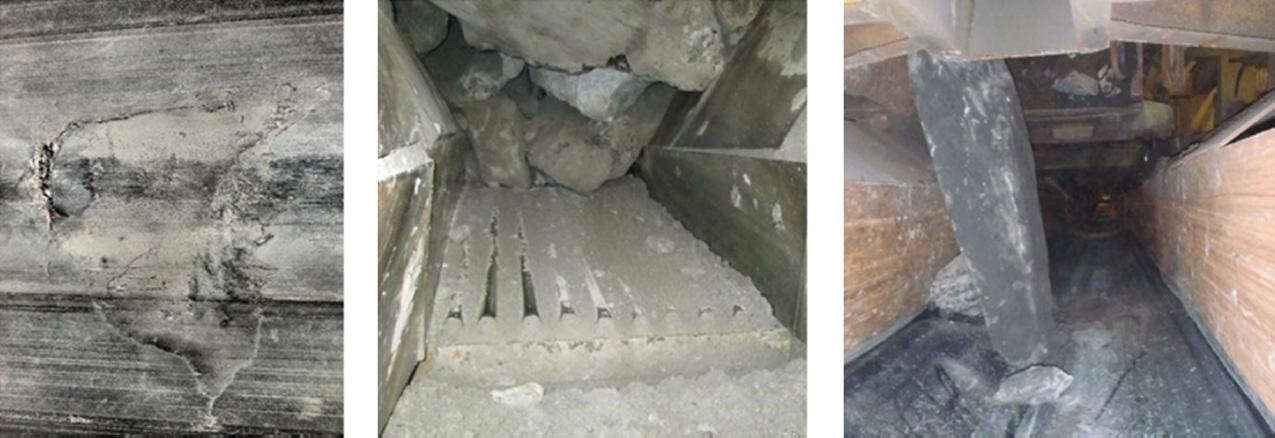
شکل 11 سوراخ شادن تسمه نقاله (a)، انسداد شوت (b)، برش طولی (c)
- مسیر تسمه نقاله: سازه مسیر نقاله نقش مهمی در پشتیبانی از تمام عناصر دوار، تسمه نقاله و مواد دارد. تمام بارهای دینامیکی و ارتعاشی ناشی از عملکرد سیستم نوار نقاله به سازه کانوایر وارد میشود. در برخی موارد، با بارگذاری بیش از حد سیستم، ممکن است ذرات سنگ روی سازه مسیر گیر کند که به نوبه خود میتواند منجر به از آسیب به تسمه، یا آسیب به قسمتهای سازهای سیستم شود که خود این مورد نیز میتواند باعث آسیب به تسمه نقاله گردد.
2- پایه رولیک و درام (عناصر دوار سیستم)
- پایه رولیکهای منحرف شده و تعداد آنها: در صورت انحراف تسمه نقاله یا کجشدن رولیکها از محور عمود بر مسیر تسمه نقاله یا به دلیل انحراف افقی تسمه نقاله (در راستای بالا یا پایین) نیروی اصطکاک اضافی بین تسمه نقاله و رولیک ایجاد میشود. این مورد باعث افزایش سایش سطح تسمه نقاله میشود.
- درام خودمحور:
- انحراف رولیکها: تراز بودن رولیکها در هدایت صحیح تسمه اهمیت زیادی دارد. خطاهای محوری کوچک نیز میتواند منجر به انحراف تسمه نقاله گردد. تراز بودن رولیکها را میتوان از سه منظر محوری، شعاعی و زاویهای بررسی کرد. انحراف باعث افزایش ارتعاش و تسریع در سایش یاتاقانها و تسمه میشود.
- پایه رولیک قفل شده: قفلشدن رولیکها منجر به اصطکاک بیش از حد بین سطح رولیک و تسمه میشود که منجر به تسریع سایش تسمه نقاله و حتی میتواند منجر به آتشگرفتن تسمه نقاله شود. دلایل قفلشدن پایه رولیک را میتوان به دو گروه تقسیم کرد: گیرکردن سنگ یا دانه بزرگ و یا گیرکردن یاتاقان. دلیل اول معمولاً به علت بارگذاری بیش از حد تسمه نقاله است، بااینحال یاتاقانهای آسیبدیده اغلب دلیل قفلشدن پایه رولیک هستند. به دلیل بارهای متفاوت، رولیکهای جانبی بیشتر در معرض آسیب هستند. یاتاقانهای فرسوده به طور قابلتوجهی بار روی درایوها را افزایش میدهند، بنابراین مصرف انرژی نیز افزایش مییابد. در شرایط عملیاتی، یاتاقانهای رولیکها در معرض بارها و ضربههای دینامیکی بالا، ارتعاش، کثیفی، رطوبت یا تغییرات دمایی بالا هستند بهخصوص آلایندهها و گردوغبار به طور قابلتوجهی عمر آنها را کاهش میدهند؛ بنابراین استفاده از یاتاقانهایی باکیفیت که بهخوبی سیل شدهاند بخصوص در محیطهای آلوده و خورنده بسیار ضروری است. البته باید در نظر داشته باشید که حتی رولیکها با بهترین کیفیت عمر سرویسدهی محدودی دارند، بنابراین نظارت مداوم بر وضعیت و تعویض دورهای آنها بسیار مهم است.
- آسیب تیوب رولیک: آسیب به تیوب رولیک معمولاً به دلیل اصطکاک بیش از حد بین پایه رولیک و تسمه نقاله رخ میدهد. این ساییدگی میتواند منجر به تشکیل لبههای تیز در تیوب رولیک شود که به نوبه خود باعث آسیب یا سایش بیش از حد تسمه نقاله میشود و به طور قابلتوجهی عمر آن را کاهش میدهد. عواملی که میتواند این سایش را تسریع کنند، ذرات مواد و کثیفی بین تیوب و تسمه نقاله و قفلشدن پایه رولیک است. این مورد زمانی خطرناک اسک که مواد چسبنده از سطح تسمه نقاله بریزد که این روند قفلشدن و سایش تیوب رولیک را تسریع میکند.
3– استفاده نادرست و شرایط کاری نامناسب
- لغزش تسمه نقاله: لغزش تسمه نقاله روی سیستم نوار نقاله یکی از مهمترین عیوب در عملکرد سیستم است. این میتواند منجر به ریختن مواد، سایش روکش تسمه نقاله، آتشسوزی یا حتی پارگی تسمه شود. اصلیترین عامل ایجاد لغزش کشش ناکافی تسمه نقاله است. در مورد نوار نقالههای طولانی، انتخاب کشش در دو نظر بسیار مهم است: برای راهاندازی و عملکرد پایدار. اگر ایجاد نیروی مناسب در تسمه نقاله امکانپذیر نباشد، کشش مؤثر تسمه نقاله را میتوان با تغییر ضریب اصطکاک بین درام و تسمه نقاله یا با افزایش زاویه پیچش (wrap angle) بهبود بخشید. ضریب اصطکاک را میتوان با استفاده از پولی لگینگ سرامیکی یا لاستیکی افزایش داد. دومین علت لغزش، سایش پولی لگینگ درام محرک است. پس از مدتزمان طولانی کارکرد تسمه نقاله، سایش سطح لاستیکی درام محرک و آج آن ایجاد میشود که باعث کاهش ضریب اصطکاک سطح درام محرک و کاهش نیروی اصطکاک میشود. عامل مخرب اصلی در این مورد، نفوذ آلودگی بین پولی لگینگ و کاور پایین تسمه نقاله است. دلیل سوم، بارگذاری بیش از حد روی سیستم نوار نقاله است. این مورد میتواند به علت حمل بیشتر از ظرفیت، یا استفاده نادرست از سیستم (مثل سرعت پایین تسمه نقاله) باشد. یکی دیگر از دلایل لغزش ممکن است قفلشدن درایو با انباشتهشدن مقدار زیادی مواد روی سطوح سازه و کاور پایین تسمه نقاله باشد.
- انحراف تسمه نقاله: علت اصلی ساییدگی لبههای تسمه نقاله اصطکاک در برابر سازه سیستم نوار نقاله به دلیل انحراف تسمه نقاله است. انحراف تسمه نقاله میتواند دلایل متفاوتی داشته باشد. حتی انحرافهای کوچک تسمه نقاله را که میتواند باعث ایجاد تماس بین تسمه و سازه سیستم شود را نباید نادیده گرفت.
- کاپینگ: یکی دیگر از عوامل انحراف تسمه نقاله کاپینگ (cupping) میباشد. این پدیده به علت ایجاد تنشهای نامطلوب در تسمه نقاله به وجود میآید. این مورد میتواند باعث بروز مشکلاتی در حرکت تسمه نقاله بر روی پایه رولیکها ایجاد کند. همچنین میتواند باعث ریختن مواد از تسمه شود. کاپینگ میتواند ناشی از بارگذاری بیش از حد تسمه نقاله، عملکرد نامناسب تنشنر یا بار ناهموار بر روی تسمه نقاله باشد.
- اتصال نامناسب: اتصال مناسب علاوه بر اینکه از نظر استحکامی بسیار مهم است، از نظر هندسی نیز بسیار اهمیت دارد. از نظر هندسی اگر اتصال به روش اصولی انجام نشود باعث حرکت غیرخطی تسمه نقاله و توزیع غیریکنواخت نیروی کشش در قسمتهای مختلف تسمه نقاله میشود. اگر اتصال بهدرستی انجام نشود تنها راهحل آن تعویض آن با اتصال جدید است. اتصال نادرست منجر به آسیب به تسمه نقاله میشود: برش طولی، گیرکردن تسمه نقاله با سازه دستگاه یا اجزای دوار، آسیبهای مکانیکی مانند ازدسترفتن چسبندگی کاور تسمه نقاله، پاره شدن منجید یا کوردهای فلزی و … .
در اتصال جدید باید به نحوه برش، نوع لایهبرداری، چیدمان صحیح، نوع رزین مورداستفاده (در آپارات گرم و سرد)، نوع فیلر، نوع دستگاه ولکانایز گرم، دمای پخت، فشار پخت و زمان پخت توجه ویژهای داشت. برای مقایسه انواع اتصالات تسمه نقاله میتوانید به لینک زیر مراجعه فرمایید.
- انتقال آلودگی از تسمه نقاله به سطح درام: تجمع آلودگی بین تسمه و درام میتواند منجر به آسیب هر دو شود. آلودگی روی درام نرخ سایش تسمه نقاله را افزایش میدهد. مواد ریز با سختی بالا (مثل شن و ماسه، سنگدانهها و …) با علت سختی بالایی که دارند باعث افزایش نرخ سایش روکش تسمه نقاله میشوند. همچنین تجمع این مواد روی پولی میتواند باعث انحراف تسمه نقاله گردد. درام اسنب، درام برگشت و درام کششی بسیار آسیبپذیر هستند بخصوص در زمانی که اجزای تمیزکننده (اسکریپر) وظیفه خود را بهدرستی انجام ندهند. همچنین مواد بین تسمه و درام علاوه بر آسیب به تسمه و درام، باعث لغزیدن تسمه روی درام نیز میشود و از کارایی سیستم میکاهد.
اسکریپر و نمونهگیرها: اسکریپرها معمولاً از تیغههای فولادی و پلیاورتان ساخته میشوند. بسیار سختتر از فولاد است؛ بنابراین برای برآوردهکردن الزامات سایشی بالا و طول عمر بالاتر اسکریپر از تنگستن کارباید استفاده میشود. پلیاورتان مادهای است که مقاومت سایشی کمتری نسبت به بقیه دارد و طول عمر کمتری دارد. در صورت نصب اشتباه اسکریپر، پلیاورتان آسیب کمتری به تسمه نقاله وارد میکند (از معدود مزیتهای اسکریپر پلیاورتان). نصب صحیح اسکریپر عامل مهمی در افزایش طول عمر تسمه نقاله و خود تیغه اسکریپر است. نصب نادرست علاوه بر اینکه باعث خراشیدهشدن سطح تسمه نقاله میشود باعث سایش زودتر خود تیغه میشود. یکی از ایرادات اسکریپرهای معمول این است که به طور یکنواخت ساییده نمیشوند و خوردگی در مرکز بیشتر است. در این هنگام اسکریپر وظیفه خود را بهدرستی انجام نمیدهد و تمیزکاری بهدرستی انجام نمیشود و مواد برگشتی منجر به آسیبهای بعدی میشود. برای بررسی انواع اسکریپرها یا پاک کننده های نوار نقاله روی لینک کلیک کنید.
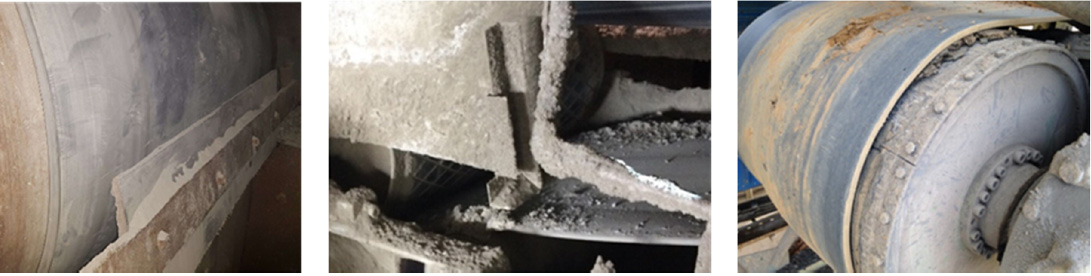
شکل 12 ایرادات ناشی از شرایط عملیاتی، استفاده از تسمه نقاله قدیمی بهعنوان اسکریپر(چپ و وسط)، تجمع مواد بین درام و تسمه نقاله
- لاستیک بغلبند نامناسب: صفحات بغلبند در هنگام بارگیری برای هدایت مواد و جلوگیری از ریزش مواد استفاده میشود. ساختار این مجموعه شامل یک قاب فولادی متصل به سیستم نوار نقاله و یک صفحه لاستیکی است. لاستیک بغلبند با تسمه نقاله در تماس است و نصب مناسب آن میتواند یک فشار یکنواخت ایجاد کند. باتوجهبه اینکه در سایش مواد، در درجه اول تفاوت در سختی عناصر در تماس تأثیرگذار است؛ بنابراین انتخاب لاستیک نامناسب میتواند نرخ سایش پوشش تسمه نقاله را افزایش دهد. راهحل مناسب استفاده از لاستیک بغلبند از جنس نرمتر یا مشابه با تسمه نقاله است. همچنین لبه لاستیک بغلبند باید یکنواخت باشد.
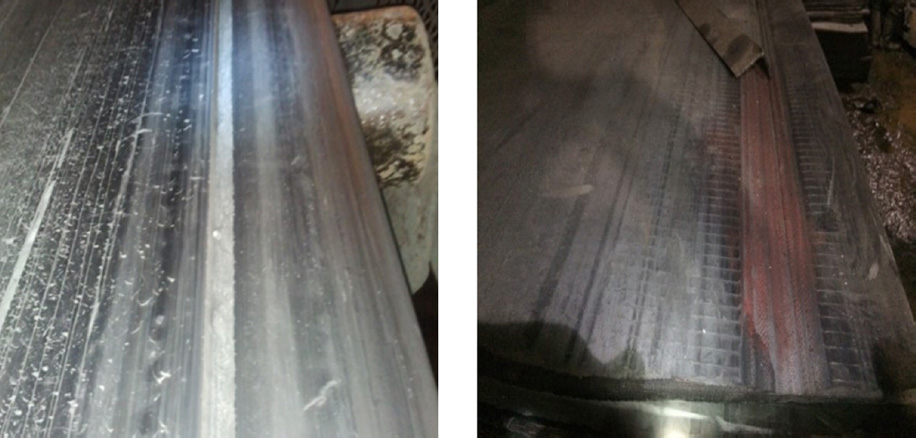
شکل 13آسیب ناشی از بغلبند نامناسب
سایر عوامل: بیشترین آسیب ممکن به تسمه نقاله در حین عملکرد وارد میشود. لاستیک بهعنوان یک ماده پلیمری بسیار مستعد ازدستدادن خواص مکانیکی خود میباشد. عواملی مثل حرارت، تابش نور شدید، تماس با مواد شیمیایی خورنده و … میتوانند زنجیره پلیمری لاستیک (تعیینکننده خواص لاستیک) را از بین ببرند. شرایط انبارش و نگهداری نوار نقاله از استفاده نیز بسیار حائز اهمیت است. لطفاً مقاله مرتبط با این مورد را نیز مطالعه بفرمایید.
گردآورنده: فرزاد شیرمحمدلی
نظرات کاربران
نظرات و پیشنهادات خود را با ما به اشتراک بگذارید